Social
Occupational Safety and Health
A number of occupational safety and health activities are carried out at our production sites in line with the Industrial Safety and Health Act combined with the individual rules of the companies.
We have introduced an occupational safety and health management system (OSHMS)* making an effort to take our occupational safety and health to the next stage. The OSHMS is a system to organizationally and systematically comply with the laws and regulations and manage the implementation of voluntary rules. By executing a PDCA cycle as a core element of the OSHMS, we will continue to step up the level of the occupational safety and health. Thereby, we prevent occupational accidents along with providing all employees with safe and healthy workplaces.
*1 The occupational safety and health management system (OSHMS) is designed to prevent labor accidents, promote workers’ health and create comfortable workplaces to raise the level of on-site safety and health by setting and implementing a plan-do-check-act cycle, or PDCA cycle, for the voluntary and continuous management of on-site safety and health. Since January 2009, Kawasaki Plant has been certified as a JISHAcompliant OSHMS-certified business site (certification no.: 09-14-9) based on the guidelines set by the Ministry of Health, Labour and Welfare.
Management system
The plant head serves as the occupational safety and health supervisor and appoints an occupational safety and health manager (from among department managers) and an industrial physician, whose roles are defined in our occupational safety and health management rules.
Also, each of the plants has the own occupational safety and health committee composed of the occupational safety and health supervisor, occupational safety and health manager, industrial physician and a representative of the labor union.
The committee meets once a month to discuss and monitor legal issues and works to raise employees’ awareness of the plant’s annual safety and health plan and monthly initiatives.
Safety records
The following figures show Nippon Yakin Kogyo’s safety record.
Compared with other industries and the steel industry overall, our rate of accidents requiring leave(frequency rate) was higher for some fiscal years. However, we have been able to maintain the rate of lost-time accidents (severity rate) at a low level for many years.
We have thus been successfully preventing the occurrence of serious accidents but have not yet reduced the number of minor accidents to zero. Zero accidents is a challenge that we should meet. Deeply recognizing the result, we will work to further improve our safety level for zero accidents.
Frequency rate
Severity rate
Quality
Nippon Yakin Kogyo produces products that meet customer needs and specifications while complying with related laws, regulations and standards. As a method for managing and increasing our product quality, we are committed to establishing, implementing, maintaining and constantly improving our quality management system that meets the requirements determined by JIS Q 9001/ISO 9001 and JIS Q 9100.
Quality policy
Kawasaki Plant is strict with the quality policy and quality assurance activity-related concept. The policy and concept are communicated across the Plant in a manner helping all on-site workers understand the details. The quality policy is intended to have the following attributes:
- Be appropriate for the purpose and situation of the Plant and help it to make progress in a strategic manner
- Provide a framework for the Plant to set the quality targets
- Include a commitment to meeting the requirements applied to the Plant
- Also include a commitment to improving the quality management system on a continual basis
Quality improvement initiatives
Nippon Yakin Kogyo is executing a PDCA cycle as provided for under JIS Q 9001 for the maintenance and improvement of the product quality. Specifically, we make a plan (P) in consideration of risks and opportunities, do (D) things as planned for the achievement of our quality targets, check (C) the improvements made, and then act (A) by reporting the results for review by the management team.
Quality assurance system
We have the Nippon Yakin Kogyo Group Quality Assurance Committee, chaired by a director appointed by the president to continuously improve the Nippon Yakin Kogyo Group’s quality assurance system. This committee is tasked with the following roles:
- Formulate policies on the improvement of the quality assurance system
- Carry out audits at Group companies’ major production bases (once a year in principle)
- Organize a meeting of Group companies’ employees in charge of quality assurance (once a year)
Standardization activities
To ensure that our products are competitive, we are actively carrying out standardization activities, registering our products for standards such as JIS. Major products of ours, including 64 , 254N and 354N , have already been made JIS-compliant.
Human Rights
Companies are required to recognize that they may have direct and/or indirect impacts on human rights through their business activities and take measures to prevent human rights infringements.
To ensure that Nippon Yakin Kogyo respects and protects the human rights of all its employees, we have established a code of conduct and anti harassment regulations to clarify appropriate behavior in the Company. We also established Nippon Yakin Kogyo Group Helpline Rules, which stipulate the internal consulting and reporting systems that must be present to promptly detect and take correct ive action against unfair acts by organizations and individuals within the Group.
In 2020, the Japanese government determined the National Action Plan on Business and Human Rights. Since then, human rights issues, including those in companies’ supply chains, have been attracting considerable attention. Nippon Yakin Kogyo is aware of the importance of addressing these issues and aims to create an even better system than those mandated by these government rules through ongoing discussions at meetings of the Sustainability Strategy Promotion Committee.
Nippon Yakin Kogyo Group Human Rights Policy
We have established the ”Nippon Yakin Kogyo Group Human Rights Policy”(the Policy) as of April 30,2024.
We have established the Policy with the aim of clarifying Nippon Yakin Kogyo Group’s thoughts regarding the respect of
human rights in business operations.
Through it, we hope to empower all employees of Nippon Yakin Kogyo Group to take initiatives on this matter.
By following this Policy, we will contribute to an inclusive society which prevents human rights violations and
discrimination.
Prevention of harassment
Nippon Yakin Kogyo has established rules to prohibit harassment and all other forms of misconduct, including sexual harassment, abuse of power and harassment of pregnant employees and employees taking maternity, paternity, parental or long-term care leave. Workplace harassment undermines personal dignity and integrity. Such unfair acts create a hostile work environment and should never be permitted.
We provide employees with education to prevent harassment and in FY2023, we conducted an online harassment prevention training seminar for all managers. We also provide employees with services providing advice about harassment, including an internal email-based service and a readily accessible external service.
To protect the victims of harassment, we have also set rules to safeguard the privacy of anyone who uses the advisory service and prevent any reprisal against them.
Human rights due diligence
The Group began carrying out human rights due diligence(HRDD) initiatives in FY2024 according to the United Nations Human Rights Council’s Guiding Principles on Business and Human Rights.
■ Management system
The specifics of HRDD initiatives are discussed by our Sustainability Strategy Promotion Committee chaired by the president. Discussions by the Sustainability Strategy Promotion Committee are reported to and supervised by the Board of Directors as necessary.
■ Process for identifying human rights risks
Scope of FY2024 assessment: Domestic Group businesses
Step 1: Human rights risks specific to this industry were identified among human rights incidents that occurred in the last five years, utilizing international criteria and guidelines and external databases.
Step 2: Among the industry-specific human rights risks identified in Step 1, human rights risks that should be prioritized were identified according to the Group’s current situation and the advice of experts. Human rights risks were identified on two axes: severity (the level of physical, psychological and lifestyle impact in the event that the risk occurs) and likelihood of occurrence.
■ Critical human rights issues and countermeasures
The table to the right shows the priority human rights issues that were identified in the human rights risk assessment. We had already been working on mitigation and prevention of the three risks that were identified, but we will continue and strengthen our activities to that end in future. Going forward, we will expand the scope of our internal investigations and carry out deliberations to identify specific human rights issues in our supply chain.
Critical human rights issues | Main countermeasures | |
---|---|---|
Development of Safe and Healthy Work Environment | The Group will develop a work environment that is easy to work in, giving consideration to health and safety. |
• Improvement of health and safety level according to OSHMS (occupational safety and health management system) and internal rules • Ongoing safety training centering on plants • Improvement of working environment with automation and labor-saving measures through strategic medium- to long-term investments |
Elimination of Discrimination and Harassment | Any discrimination by employees and related parties due to any attributes not related to duties to be performed, including race, ethnicity, gender, status, gender identity, sexual orientation, language, religion, political and other opinions, nationality or social origin, assets, birth, disabilities, illnesses, and other conditions, and form of employment, is prohibited. In addition, the Group does not tolerate abuse of power, sexual harassment, or any other form of action or speech that harms individual dignity. |
• Establishment of regulations and training on prevention of harassment • Thorough communication about internal reporting systems and harassment consultation services |
Responsibility to Communities | The Group recognizes that business operations may directly or indirectly impact human rights in local communities, and in addition to not using conflict minerals linked to human rights abuses, the Group will respect the environment and residents’ land rights in the areas surrounding those related to business operations, including ensuring rights relating to prevention of pollution and the right to water and other resources. | • Stringent environmental management according to ISO 14001 and internal rules |
■ Training of employees
Nippon Yakin Kogyo conducts human rights training for Group employees to facilitate human rights activities according to our Human Rights Policy. In FY2024 and FY2025, we have been holding presentations on human rights risks and our Human Rights Policy and writing articles in our in-house magazine about international trends in business and human rights and measures that should be taken.
■ Consultation services
The Group has established Nippon Yakin Kogyo Group Helpline Rules under which we accept consultations and reports about human rights risks such as harassment. We have established and enforced rules such as stringent confidentiality practices for reports and consultations and prevention of retaliation against those who make a report or consultation.
Refer to "Internal reporting system (Helpline)" for details
https://www.nyk.co.jp/en/sustainability/governance.html#compliance
Promotion of diversity, equity and inclusion
One of Nippon Yakin Kogyo’s action guidelines is “We respect diversity and differences, and demonstrate our comprehensive capabilities with a spirit of harmony.”
According to the results of a survey conducted by the Ministry of Internal Affairs and Communications, Japan’s working population has been decreasing since reaching a peak in 2008 and will continue to drop at an accelerating rate.
Against this backdrop, women and older people are increasingly expected to join the workforce. Also, in line with the changes of the times, values have become diversified and a range of flexible work arrangements are needed. We believe that respecting the diverse backgrounds and ideas of employees and enabling all employees to thrive here will help us achieve sound growth and are promoting diversity, equity and inclusion in the workplace accordingly.
Employment of people with disabilities
Nippon Yakin Kogyo also fosters the employment of people with disabilities for the creation of a society where all people can make valuable contributions. Kawasaki Plant provides the employees with disabilities with a special office space where they can work in comfort, as well as dedicated support personnel, giving due consideration to their individual characteristics.
Promotion of empowerment of women
We are taking the following measures to further promote empowerment of women.
- (1)Active hiring of women and appointment of women in
diverse roles
First, we have set the target of increasing the rate of women hired in career-track positions to at least 20% of the total number of new hires. Three out of the 15 career-track employees who joined the Company in April 2024 are women. -
(2)Promotion of the building of working environments where women can work comfortably
We have 12 female production operators as of April 2024. To help them work in greater comfort, we have introduced electric tools, workbenches and lifters to reduce the physical load imposed on them, and have provided female-only showers and powder rooms.
Action Plan Based on the Act on Promotion of Women's Participation and Advancement in the Workplace
1 Period | April 1, 2022 to March 31, 2025 |
---|---|
2 Our challenges |
|
3 Targets |
|
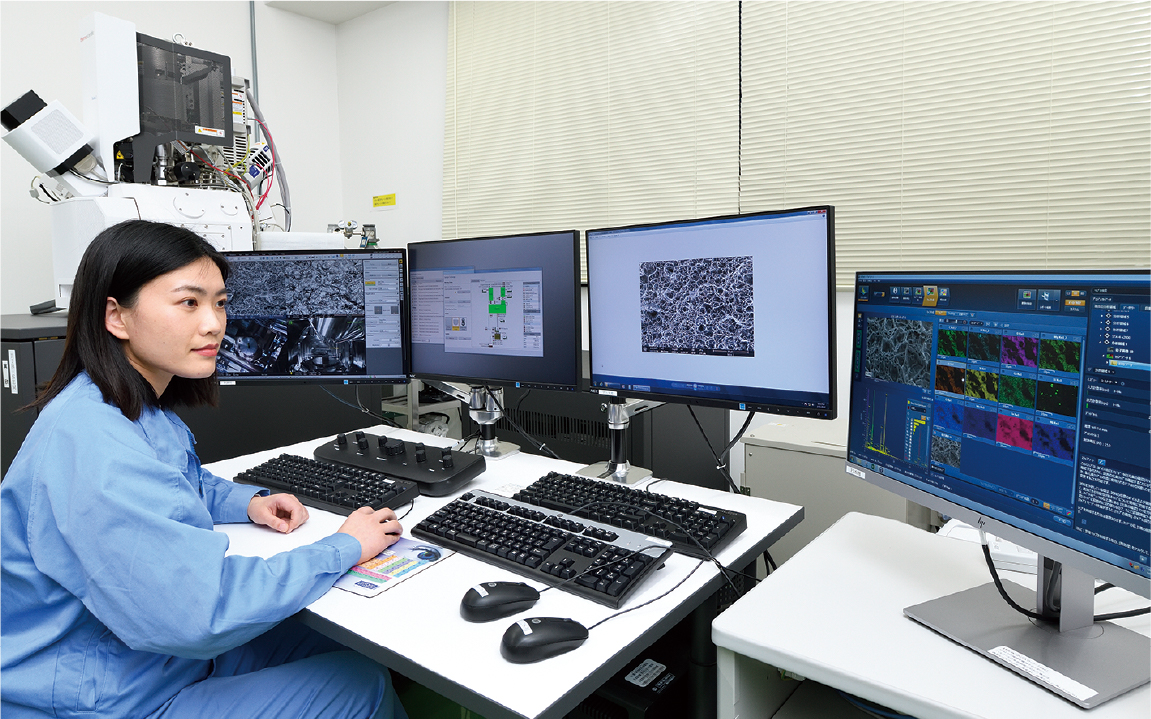
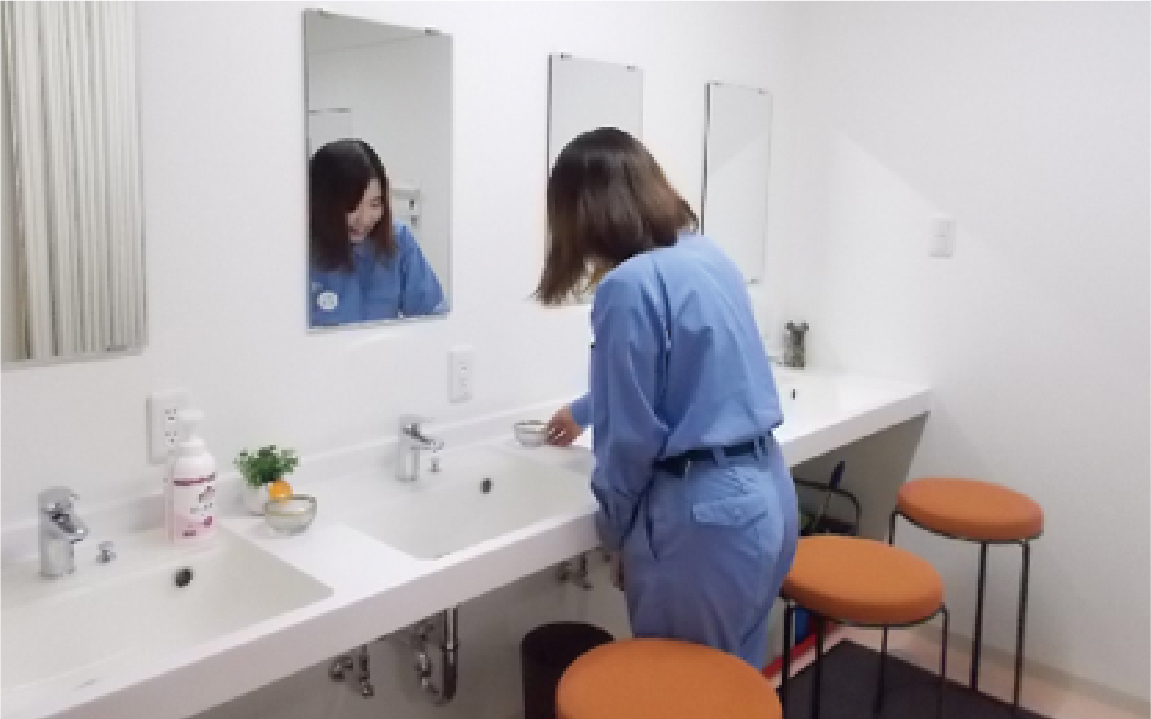
Powder room for exclusive use by female employees
Retirement age raised to 65
In April 2023, we raised our retirement age to 65 and transitioned to a new personnel system.
【Background】
In the past, employees could receive what we could call full old-age pension from age 60, and like many other companies, many of our employees retired at the age of 60.
However, the pension is now paid from age 65 and people are living for longer: we have entered an age of 100-year-olds. Because of this, many people want to work past 60, and like other companies, we have introduced a reemployment system under which, as a general rule, all employees who wish to work until age 65 can do so. However, our systems were not fully prepared to handle employees continuing to work past 60 with the same motivation as before under our reemployment system, and many employees join us mid-career instead of as new graduates, meaning that in an increasing number of cases, including those of current employees, it is not possible to handle employees in a unilateral way connected to their age.
Based on this, we have revised our entire personnel system, including discontinuing systems like our qualification system which were based on years worked here, and transitioned to system where current effort and results are rewarded from the time the employee is hired to the time they turn 65.
Human Resource Development
Nippon Yakin Kogyo Group’s products are made possible by the experience and technology that our employees have developed over the years. To facilitate further growth of the Group, we have established a Human Resource Development Policy and are working to ensure that diverse employees can thrive.
Career-track employees: Collective training
To develop employees who will be core personnel in future, we consider new graduates’ first three years at the Company to be a time for building the foundations and their fourth and fifth years a time to move to new levels. Rank-based training is provided so that employees can start from the basics and then make qualitative and quantitative improvements.
Career-track employees and production operators: one-on-one meeting system
From FY2024, we have introduced a one-on-one meeting system to foster active communication and facilitate human resource development tailored to each employee’s characteristics. One-on-one meetings are held regularly and provide employees with the opportunity to ask questions about minor matters in their work and hear about potential directions their career could take and the Company’s expectations of them, which encourages autonomous growth by each employee.
Career-track employees and administrative employees: e-learning
We have a system to help career-track employees develop their abilities with a sense of ownership of their skill
development. As a part of the system, we provide them with online video training. We have thus improved the environment
for learning by providing opportunities to learn on a daily basis without restriction of when and where, different from
the conventional education style.
Under the system, employees can choose subjects for themselves depending on their job duties.
Career-track employees: Financial support for capacity building
We provide the financial support to take external training to encourage career-track employees who aspire to be manager candidates or experts in practical operations to independently acquire additional skills outside of their jobs. This includes external training, correspondence courses, and book purchases to boost their management, leadership, and language skills, financial skills, and accounting knowledge, and increasing their IT literacy.
Production operators: Skill succession and development for production operators
For production operators, we clarify the skills necessary for them to perform their jobs and formulate specific
development plans to help them acquire those skills through OJT and OFF-JT. We use an evaluation table to centrally
manage their education to help them develop the skills they need.
We also recommend technical certification exams and create an environment where employees can train in-house.
For new employees, we have a training system called “shop adviser” under which they receive one-on-one education from
senior staff members as OJT from the end of their three-month collective training to the end of their second year.
Through this system, we hope to better motivate new employees while also helping them promptly acquire the necessary
skills as they gradually adjust to the workplace.
In our safety education, we make effective use of VR technologies to provide trainees with virtual experiences of work
hazards in a safe and immersive manner, thereby preventing accidents and raising their safety awareness.
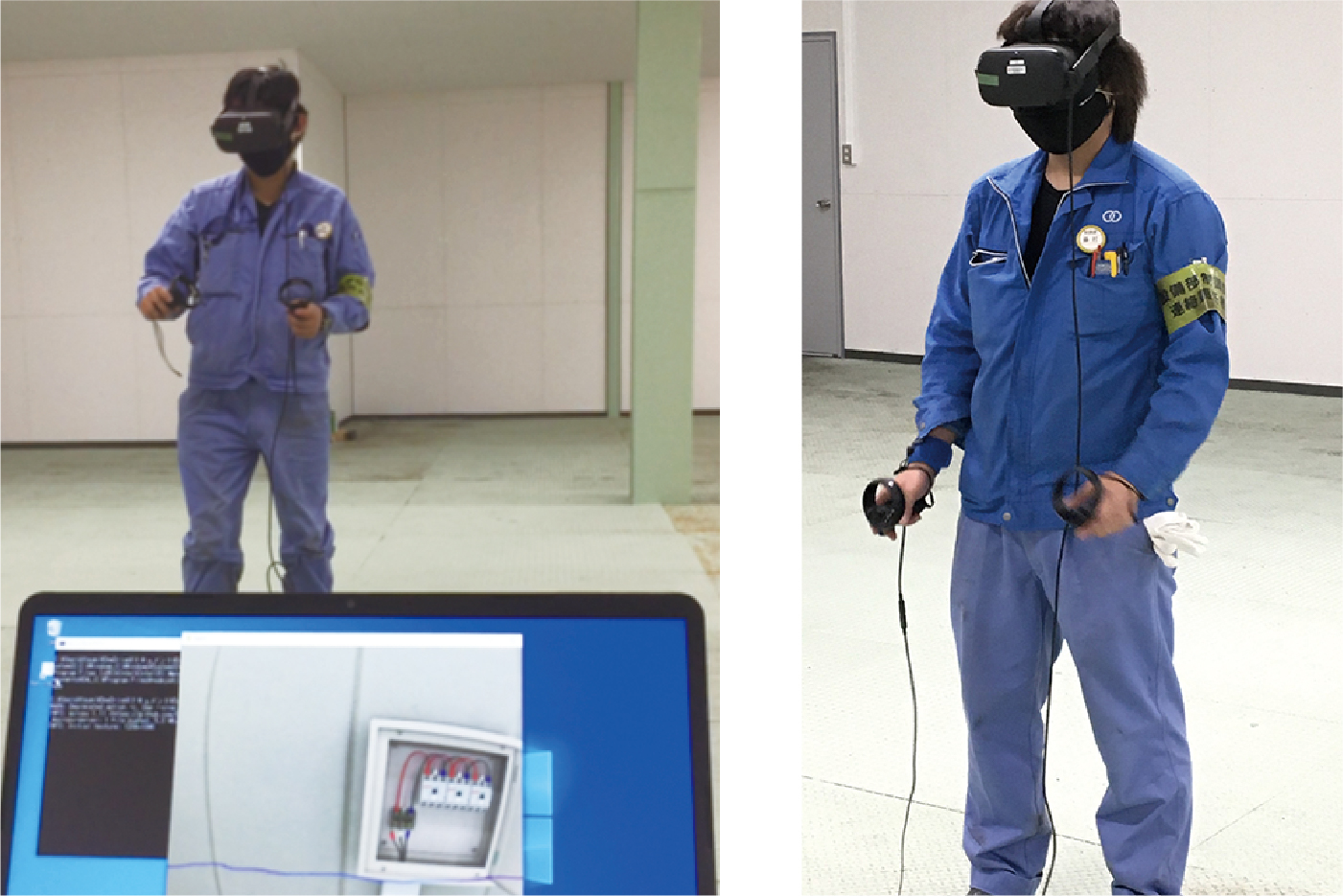
Hands-on safety training using a VR system
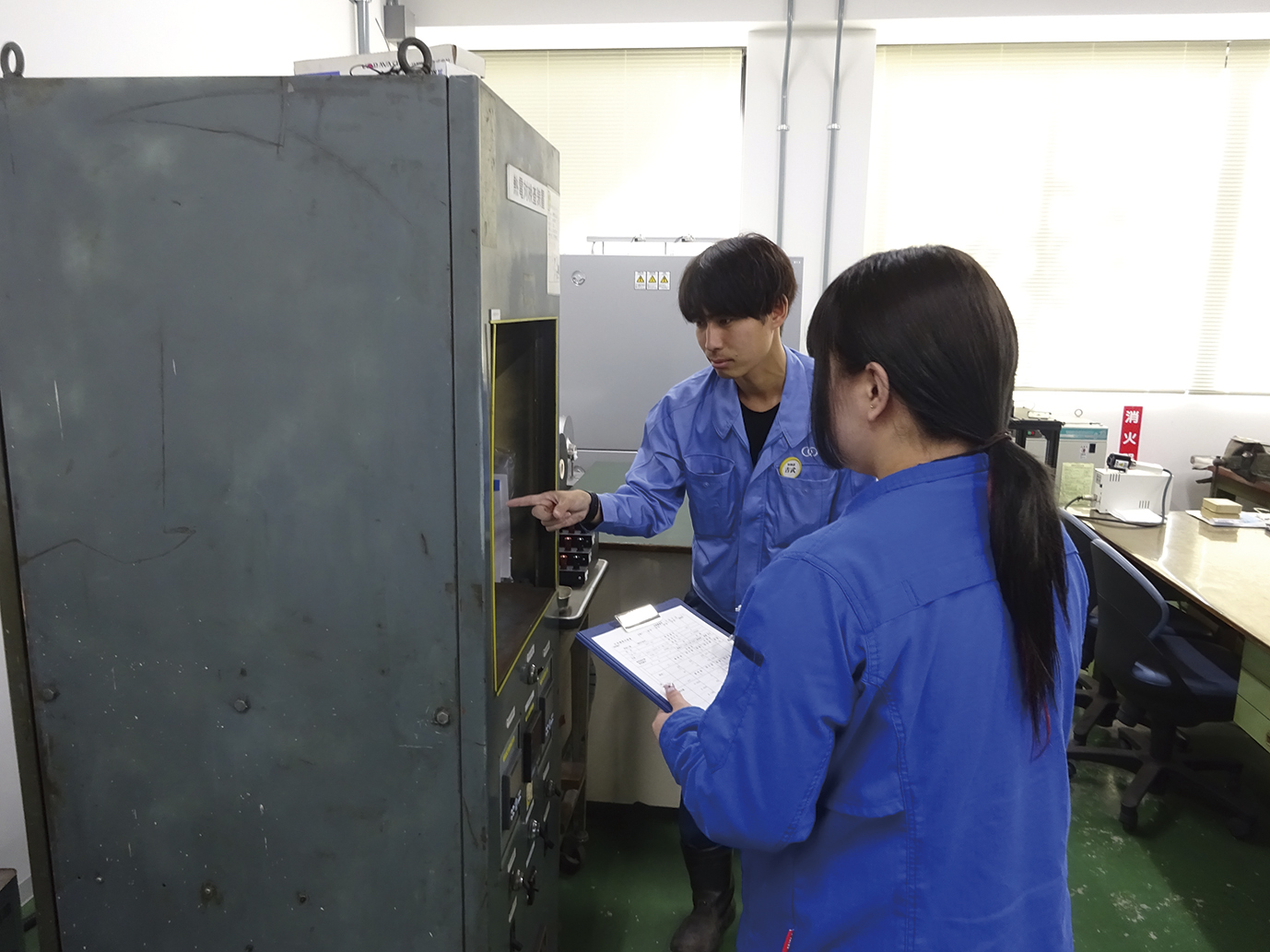
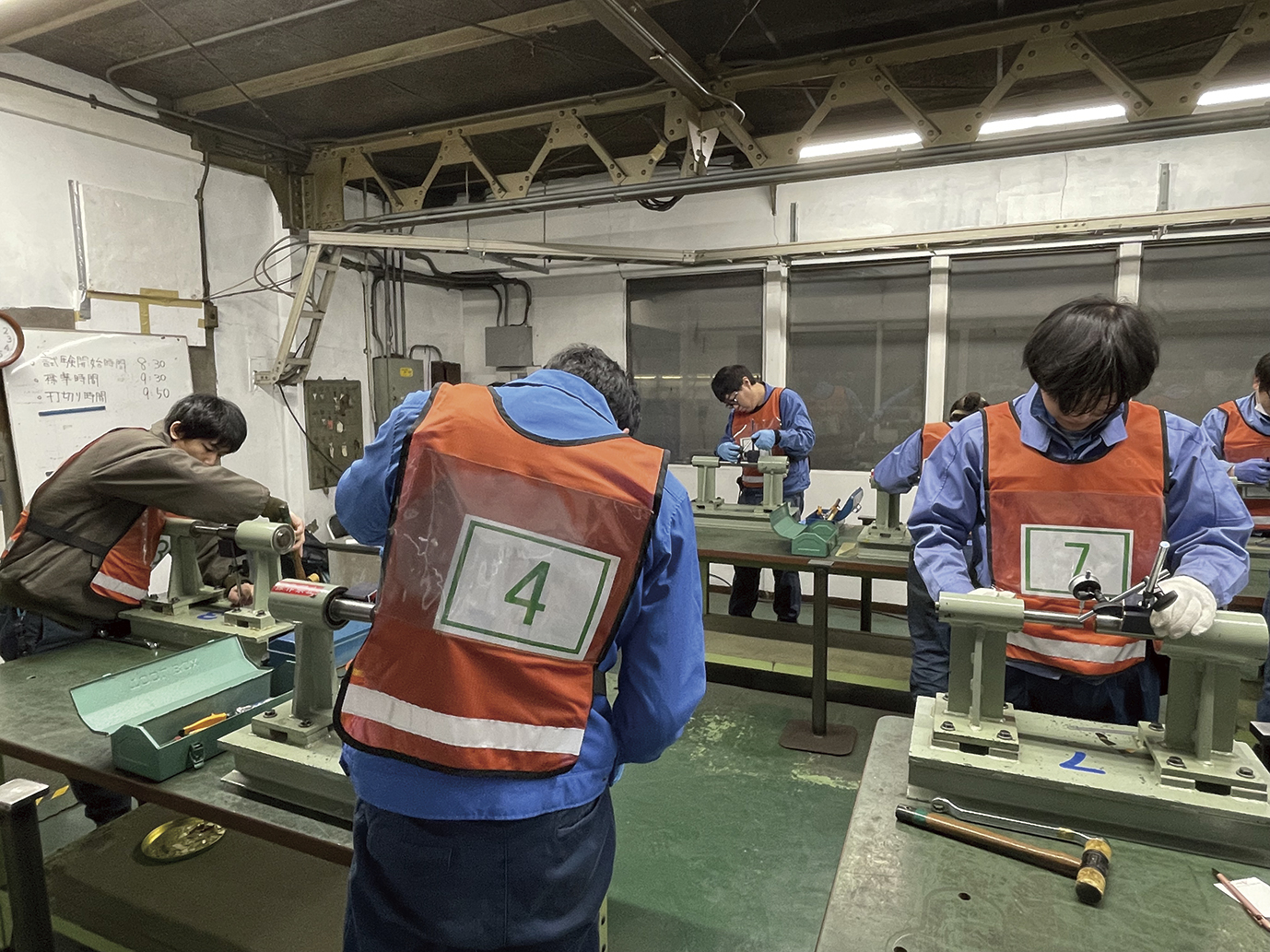
Program for studying at the College of Industrial Technology
We have a program allowing employees who have graduated high school or are equivalently skilled to study at the College of Industrial Technology to receive a specialized technical education and become technical employees with both an academic and professional insights. After studying at the College of Industrial Technology for two years, we expect to see these employees in a wider range of career-track roles.
Measures for Work-Life Balance
We are implementing measures to help employees maintain a work-life balance so that they can perform their duties and achieve job satisfaction while also spending time outside the workplace meeting family responsibilities, participating in their local communities and pursuing personal goals, thereby leading a healthy and fulfilling life.
Results concerning the major systems and initiatives
Results concerning the major systems and initiatives
Mental health measures
To help each employee to keep working in good physical and mental health, we are implementing measures to help them ward off mental illness and detect any issues at an early stage. We conduct a stress check test of employees every fall and annually provide employees in charge of occupational safety and health at each of our workplaces with mental health training.
Stakeholder Engagement
Communication with local communities: social contribution activities
Nippon Yakin Kogyo, under the leadership of Kawasaki and Oheyama Plants and in cooperation with the related Group companies, communicates with local residents to help them deepen their understanding of the Company and to contribute to the creation of a safe and comfortable living environment and the revitalization of local communities.
Kawasaki Plant
Inari festival
The Plant has an Inari shrine on the premises where we hold a festival every year on November 3. We invite local residents to attend the festival, at which we pray for the safe operation of the Plant and for the safety of the local area and also dedicate a dance to the god of the shrine.
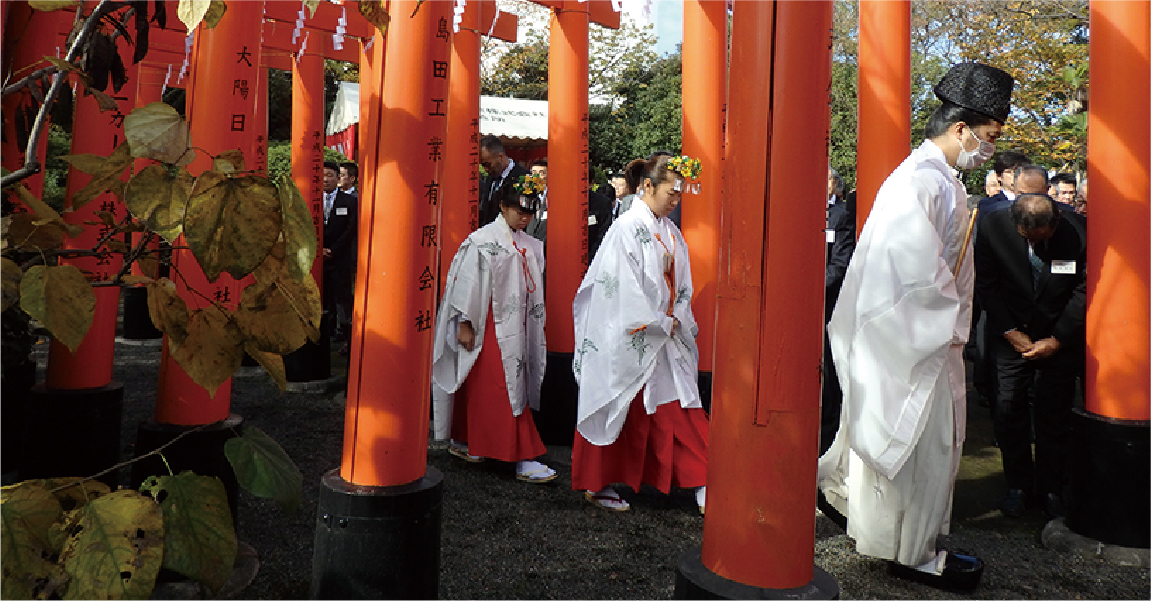
Summer festival
Together with the labor union, Nippon Yakin Kogyo annually holds a summer festival to reward employees for their efforts and to promote exchange with the local residents’ associations and others related to the company.
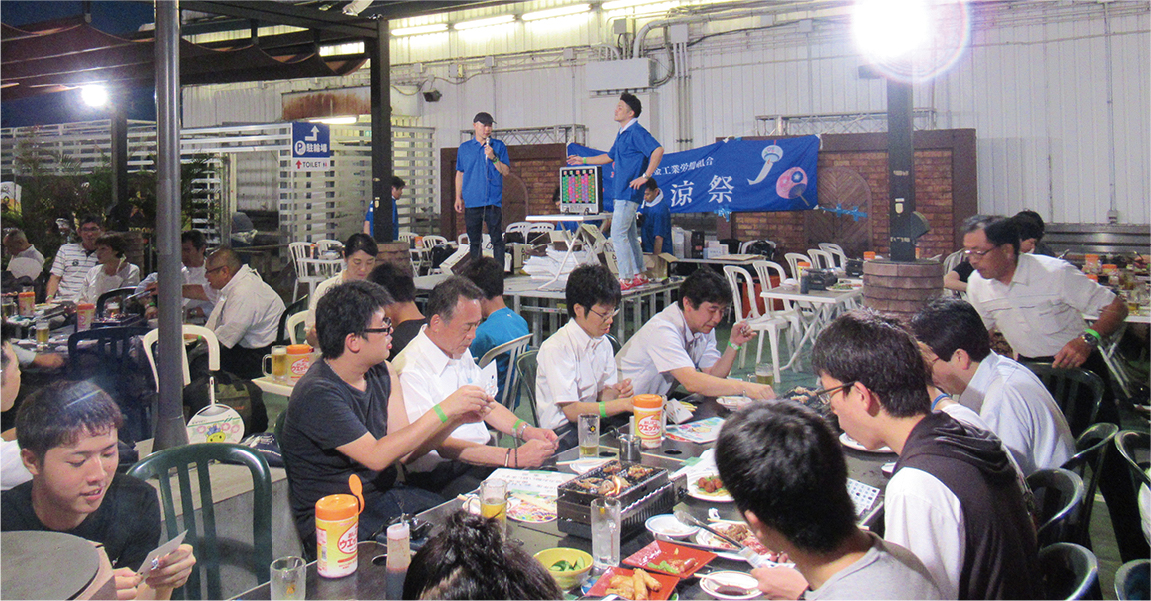
Clean-ups of nearby roads
Employees of Kawasaki Plant conduct a clean-up activity on the sidewalks of the Itsukushima Bridge [overpass] and Tonomachi Yakosen near the Plant twice a month.
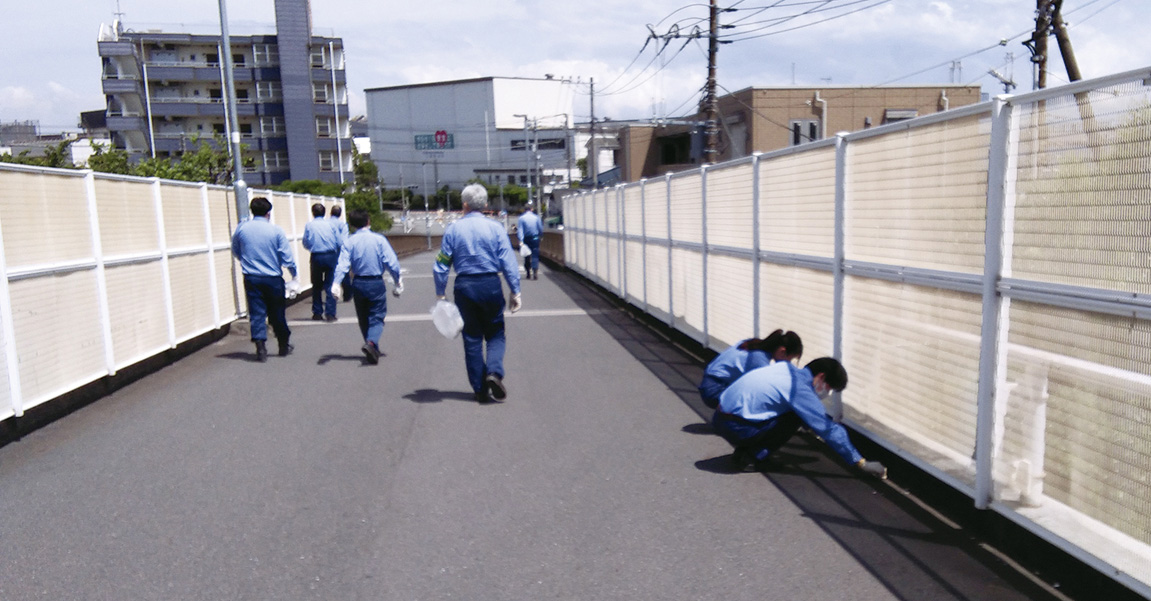
Involved in Kawasaki City 100th Anniversary Commemorative Project National Urban Greening Kawasaki Fair
2024 marked the centennial anniversary of Kawasaki City. To celebrate this milestone and highlight greening of cities around Japan in 2024 and 2025, the city held the Kawasaki City 100th Anniversary Commemorative Project National Urban Greening Kawasaki Fair. Our Kawasaki Plant was a part of the fair’s Executive Committee, as well as being a Silver Sponsor.
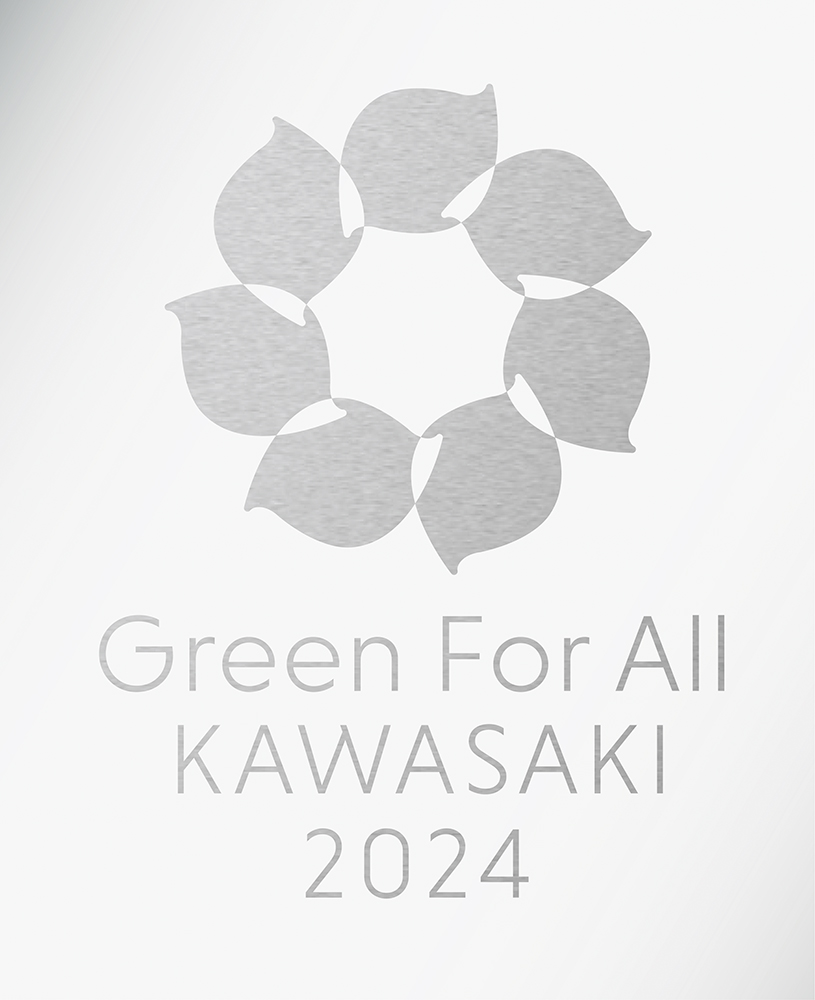
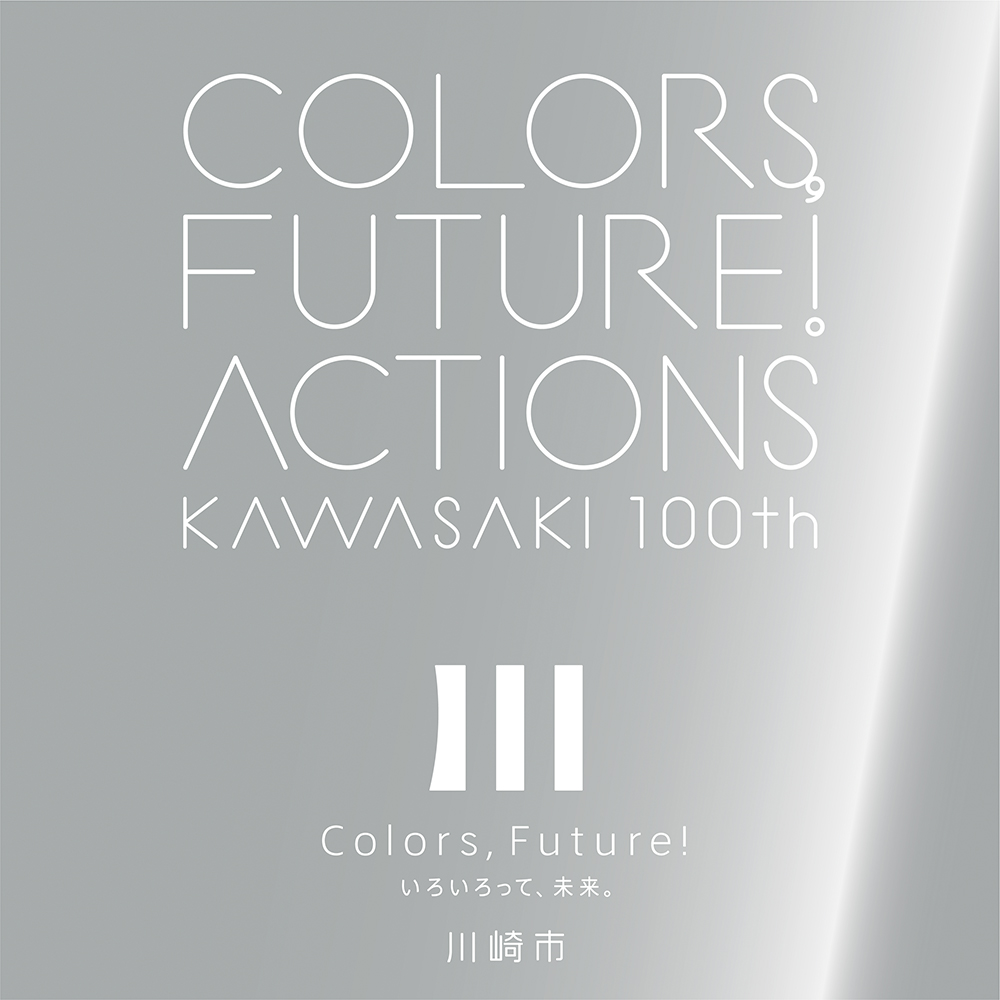
Involved in community sports events by neighborhood associations
Our Kawasaki Plant is involved in friendly sports events organized by neighborhood associations (simplified volleyball matches between neighborhood associations and local companies). Plant personnel are working to foster closer ties with members of the community and other local companies through sports and, in doing so, invigorate communities.
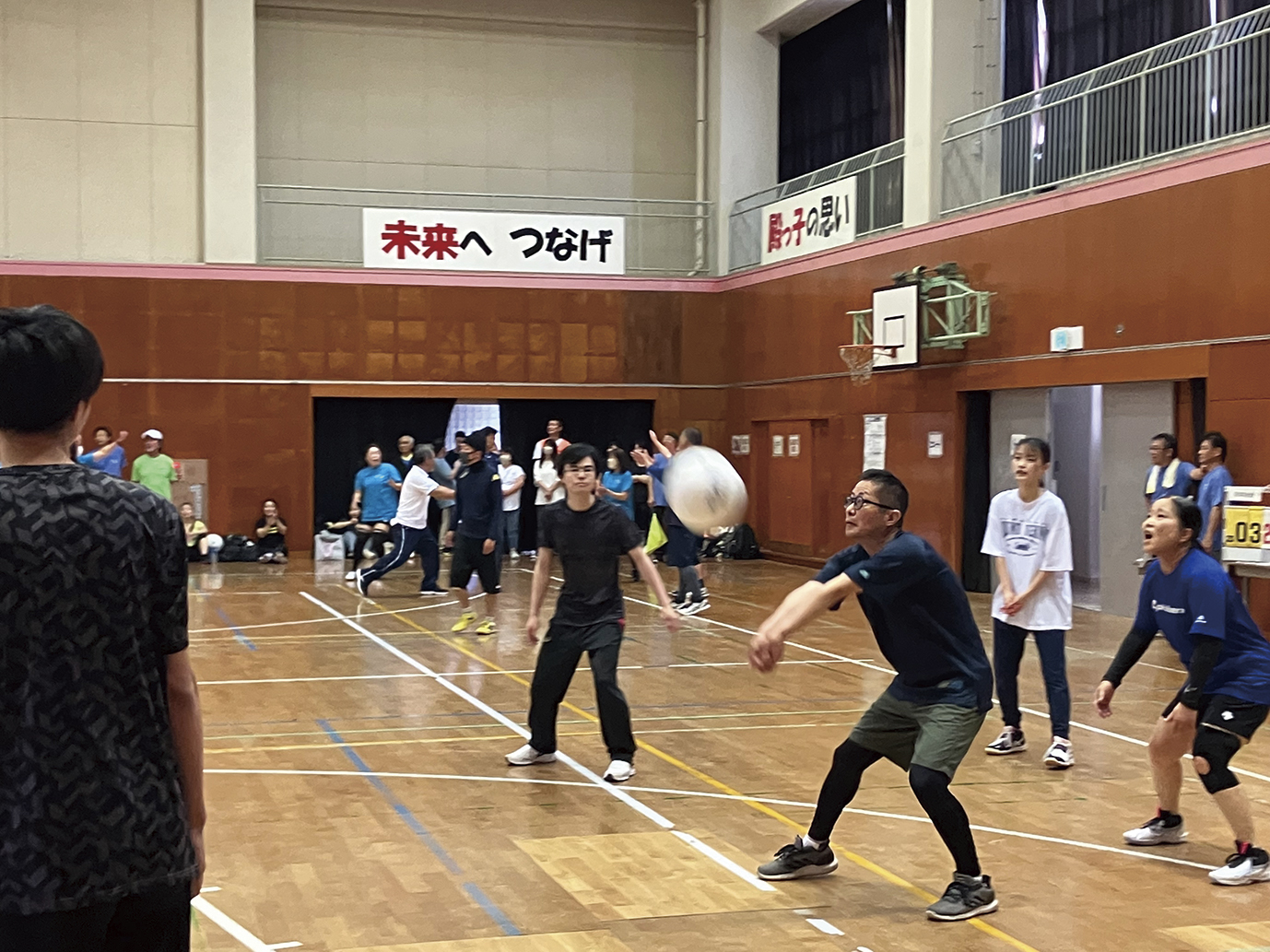
Oheyama Plant
Plant tours
Our Oheyama Plant offers tours for business partners and families of employees, as well as factory tours for students at
local elementary, junior high, and high schools.
These tours foster a greater understanding of the plant’s business among members of the community and make the plant a
more familiar presence.
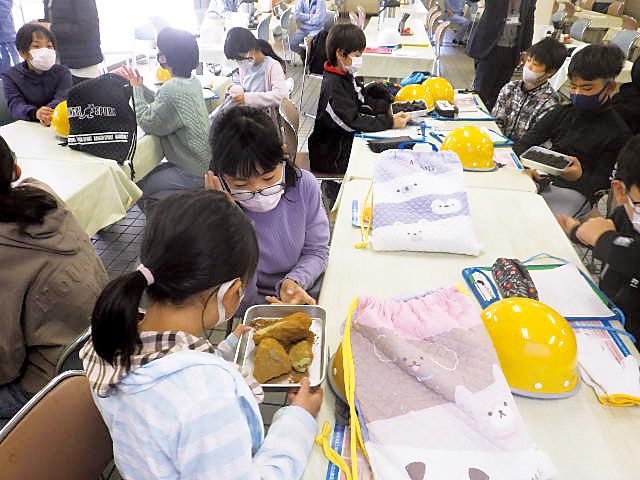
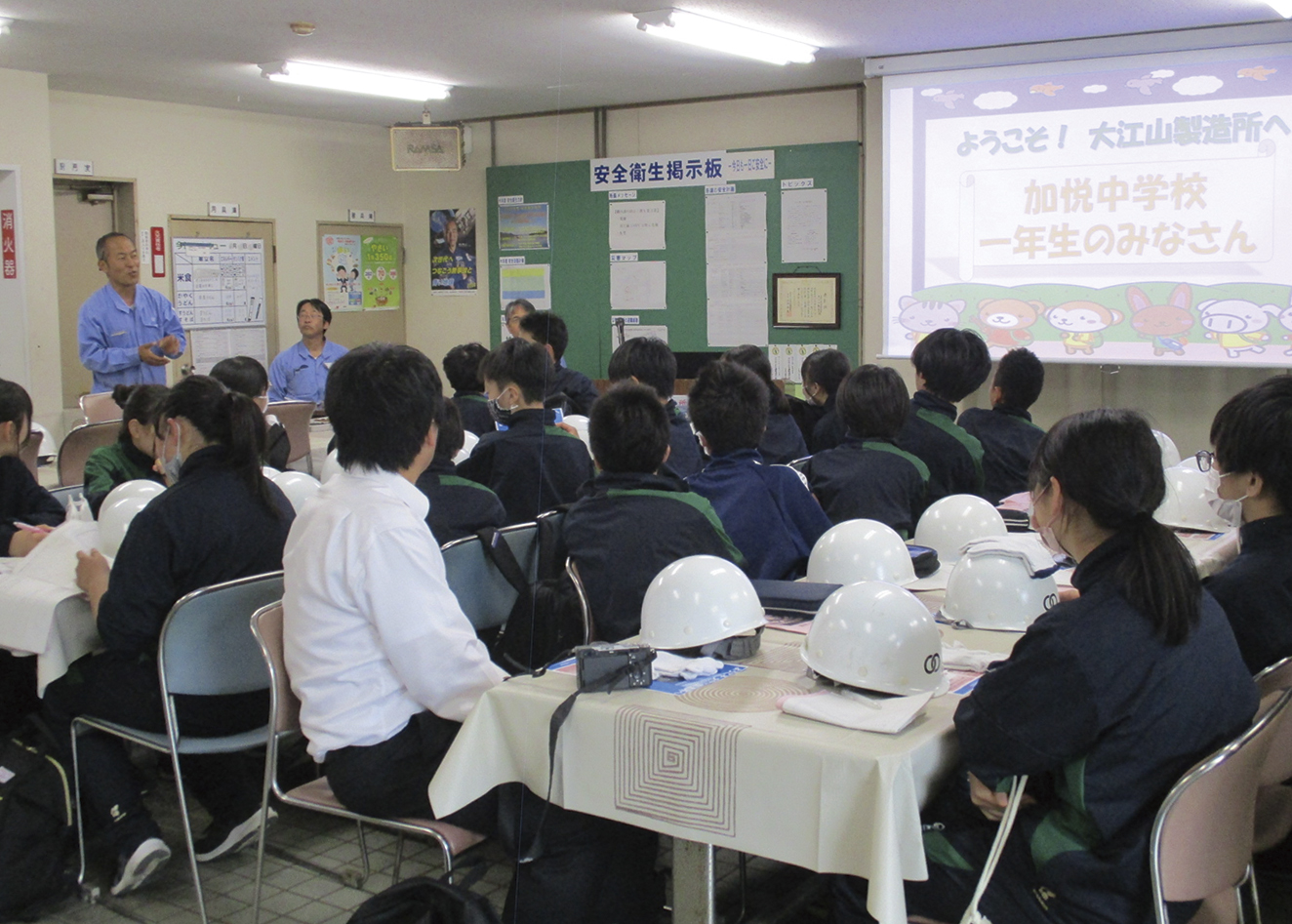
Clean-up activity for the Amanohashidate sandbar
We participate in clean-up activities of the Amanohashidate sandbar, which is regarded as one of Japan’s three most scenic views, every spring and fall for the beautification and protection of the scenic beauty. This time around 70 people participated in the acivities collaborating with local youth baseball team.
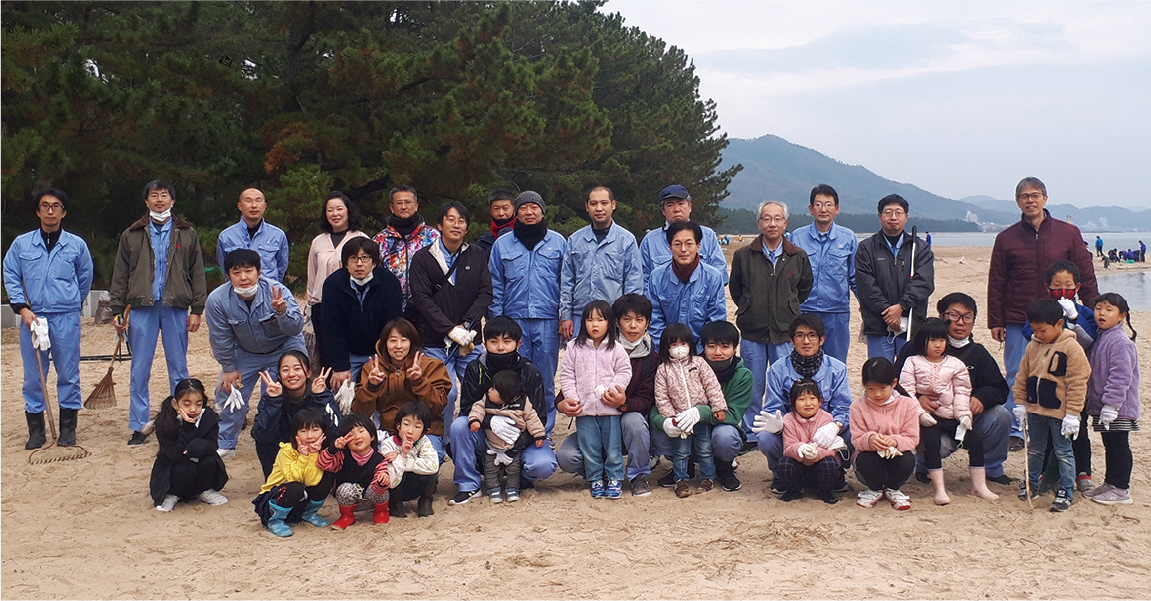
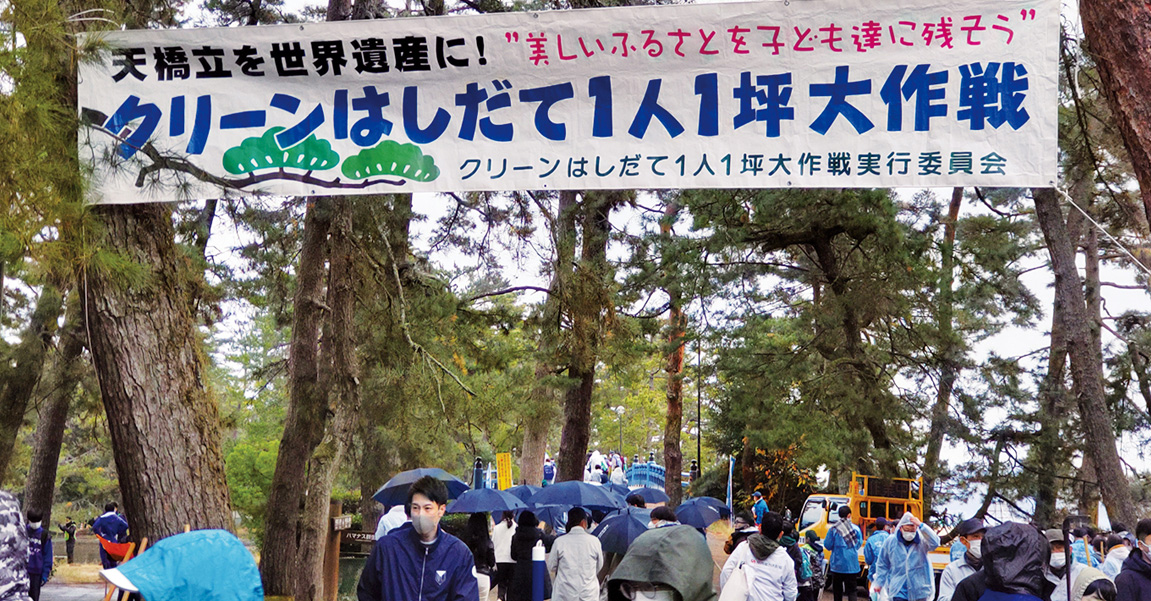
Communication with shareholders and investors
To further increase the Company’s corporate value, we disclose information to shareholders and investors as and when necessary and are working to further enhance our disclosures. At our twice-yearly briefing sessions about our financial results, we facilitate exchanges of opinion about our financial results and management plans and speak one-on-one with institutional investors (dialogues: 43 in FY2023→62 in FY2024). Feedback we receive is shared with our management team
and relevant internal divisions and relayed to our Board of Directors through our Investor Relations Committee.
We also held tours of our Kawasaki Plant for individual and institutional investors in 2023, where we showed them our equipment and explained our business strategies.
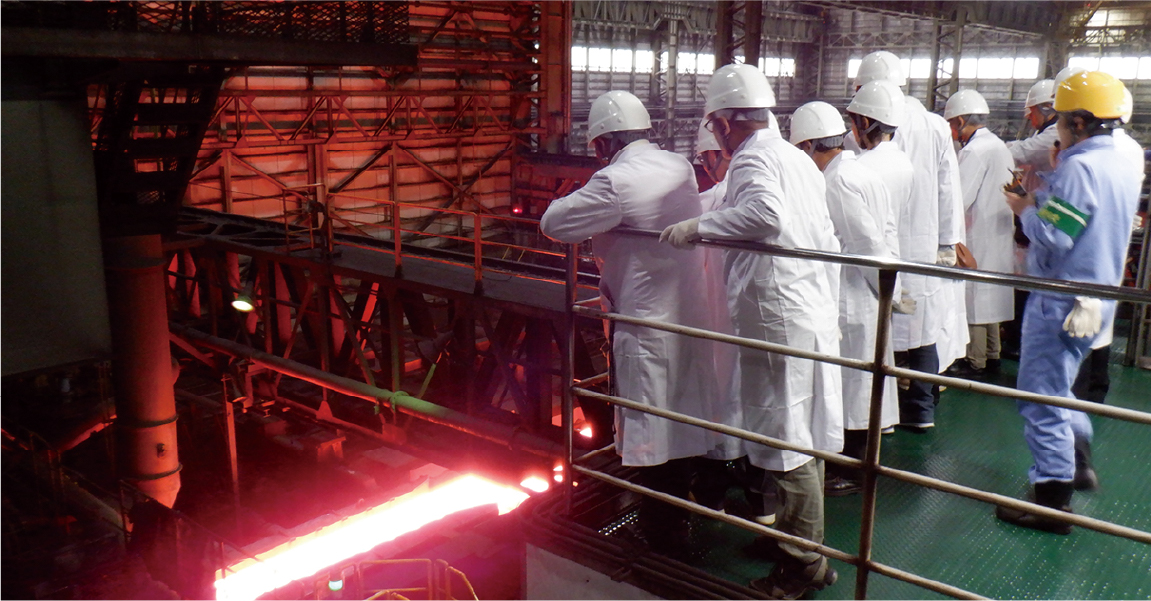
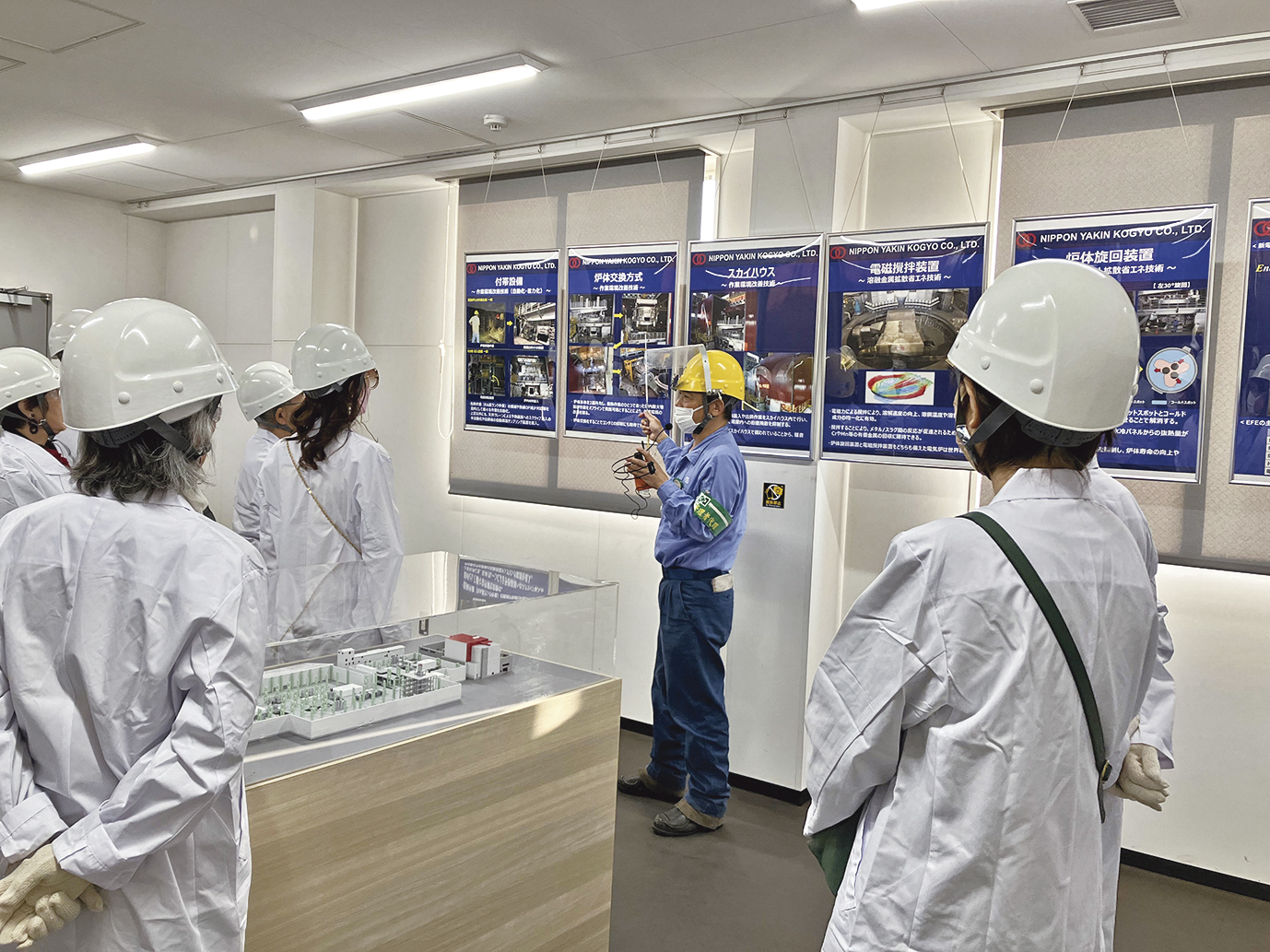
Communication with customers
As we are required to supply products that meet the needs of our customers, we aim to continuously earn their trust by providing the industry’s top-level products and services in terms of quality, due dates, cost, and technologies and solutions in order to be a sustainable company.
Our products have a significant effect on the quality and performance of the final products made by customers. Accordingly, it is essential for us to communicate appropriately with our customers at the consulting stage, before we receive orders from them, and subsequently, including at the manufacturing, delivery and follow-up stages. While responding to changes in the market environment including the trends for globalization and carbon neutrality, we are sincerely working to meet our customers’ requests from a long-term viewpoint.
For the provision of solutions, we are fostering communication with customers mainly through the Material Solutions Sales Department. We offer advice on product selection based on sample testing and property confirmation, guidance on processing and welding methods, and proposals that utilize our database and technical knowledge. Moreover, we closely cooperate with our customers for product improvements and the development of new products, thereby building even stronger relationships with them.
Communication with labor union
The Company holds “Labor-Management Roundtable Meetings” for management and labor union to exchange opinions on
management conditions, the labor environment, and other issues.
The dialogues between management and the labor union helps to build cooperative labor-management relations.
Procurement
The movement for responsible mineral procurement in global society not only includes measures against conflict minerals; it has rapidly expanded to all mineral procurement, including human rights due diligence and addressing ESG risks in supply chains. As a result, the scope of minerals, risks and regions is growing. Additionally, with moves such as the establishment of the National Action Plan on Business and Human Rights in various countries in Europe and North America, companies are increasingly obligated to perform human rights due diligence in their supply chains. Based on this, there is a growing call from stakeholders for companies to perform human rights due diligence and address ESG risks throughout their supply chains.
Like other companies, we are working to achieve responsible mineral procurement, paying attention to movements in government policy and industries in various countries and working together with various departments to strengthen our initiatives.
Management of conflict minerals
We have established the Conflict Minerals Management Rules (hereinafter, “the Rules”) for the management of so-called Conflict Minerals (i.e., gold, tin, tantalum, tungsten, and other minerals themselves, or alloying materials containing such minerals).
Under the Rules, we do not purchase from the Democratic Republic of the Congo, surrounding countries, or other conflict zones or high-risk areas. Information on conflict minerals is gathered from our raw material suppliers through the vendors we deal with, and is stored for seven years.
The Export Trade Control Committee manages the Company’s responses to conflict minerals, which are also examined through internal auditing. Details of our activities are also reported at management meetings.
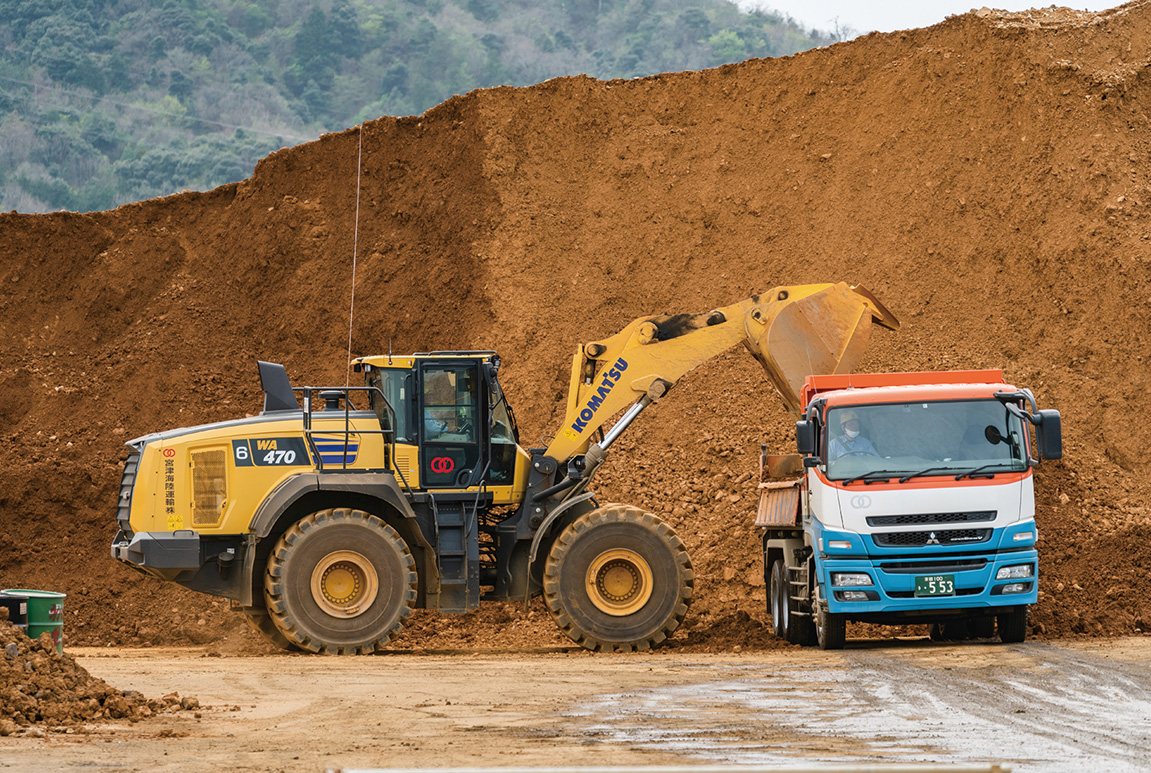
Human rights due diligence, etc. across the supply chain
Our rules and regulations incorporate mechanisms to gather information from business partners about raw materials, secondary materials and other supplies connected to countries and regions requiring human rights due diligence, such as procurement from the Xinjiang Uyghur Autonomous Region or companies involved in forced labor by Uyghurs. In April 2024, we announced the Nippon Yakin Kogyo Group Human Rights Policy, and we are working with our suppliers as appropriate on efforts to uphold human rights.
Response to environmental issues, etc. in procurement supply chain
In recent years, there have been cases of “illegitimate yards”, which store or work with illegal scrap metal and impact local communities’ quality of life through harm such as noise, vibration and water pollution. These are becoming a major social issue. In October 2023, to facilitate more stringent compliance with laws and regulations, including at supplier sites, we announced a policy that scrap metal from “illegitimate yards” must not be accepted, and asked our business partners to thoroughly manage the operations of parties such as their suppliers to ensure compliance.
Response to the 2024 Problem in Japan’s logistics
To ensure reliable and sustainable logistics, we are working together with business partners and logistics companies
according to the Japan Iron and Steel Federation’s Voluntary Action Plans toward Optimization and Productivity
Improvement in Logistics on measures such as shortening cargo wait times and loading times, improving the efficiency of
transportation, and revising and clarifying the terms of contracts to further strengthen our relationships with these
companies.
The Company agrees to the promotion of “white logistics” and has submitted a Voluntary Action Declaration.
Declaration of Partnership Building
Nippon Yakin Kogyo has agreed to the statements by the Council on Promoting Partnership Building for Cultivating the Future, comprising the Chairman of the Japanese Business Federation, the Chairman of the Japan Chamber of Commerce and Industry, the President of the Japanese Trade Union Confederation and relevant ministers (Cabinet Office, Ministry of Economy, Trade and Industry, Ministry of Health, Labour and Welfare, Ministry of Agriculture, Forestry and Fisheries, Ministry of Land, Infrastructure, Transport and Tourism), and announced its own Declaration of Partnership Building in June 2022.
To build new partnerships with the business partners in our supply chain, we will form alliances beyond factors such as our existing business relationships and the scale of our business with the aim of achieving mutual prosperity for Nippon Yakin Kogyo and its business partners. These partnerships will also include support such as business continuity assistance in cases such as disasters and advice from the perspective of work practice reforms.
We also uphold suitable practices for trading with subcontractors (Development Standards based on the Act on the Promotion of Subcontracting Small and Medium-sized Enterprises), actively and continuously work to correct trade and business practices that prevent the building of partnerships with business partners, and work to build a sustainable society and a resilient company under our management philosophy of “We promote the well-being of all who join with us”.