Environment
Environmental Management
We are well aware of the importance of environmental protection. We promote environmentally friendly business complying with environmental treaties, laws, regulations, etc. In addition, we are proactively implementing environmental initiatives, including effective use of resources, saving energy and facilitating green procurement.
Environmental management system
We have the Environmental Committee, chaired by a director appointed by the president to smoothly progress with environmental management by Nippon Yakin Kogyo and the Nippon Yakin Kogyo Group.
The Committee deliberates on and reports the environmental management plans implemented at our two plants and the issues related to energy conservation.
Kawasaki and Oheyama Plants have standardized ISO 14001/JIS Q 14001 environmental management systems.
Environmental management system
Environmental policies
We have implemented measures for our plants to achieve the environmental policies and environmental management planned by the Environmental Promotion Committee of the plants.
-
Oheyama Plant
Oheyama Plant, Nippon Yakin Kogyo’s production base for ferro-nickel, a raw material of stainless steel essential in industry and daily life, aims to contribute to society through environmentally conscious production activities.
We conduct environmental preservation activities with recognition of the location of our manufacturing site near Amanohashidate, one of Japan’s three most scenic views.
- All employees engage in environmental preservation activities. We set environmental objectives and targets, regularly revise them, and strive to improve our environmental performance on an ongoing basis.
- We comply with laws, ordinances, agreements, and other matters concerning environmental preservation, set voluntary standards and strive to improve our environmental preservation.
- We strive to prevent environmental pollution through recycling and resource and energy conservation based on our environmental preservation activities that give consideration to life cycle management.
- We communicate our environmental policy to all people who work at the plant, and maintain our environmental management system through employee education on our environmental objectives and targets.
- We strive to act in cooperation and solidarity with the local community for the promotion of environmental preservation activities.
Executive General Plant Manager of Oheyama Plant, Nippon Yakin Kogyo Co., Ltd.
-
Kawasaki Plant
The Kawasaki Plant, Nippon Yakin Kogyo’s production base for specialty stainless steel products that are the foundation of industry and daily life, aims to contribute to building a creative society by continuing to provide products that deliver true customer satisfaction through manufacturing and development with consideration for environmental preservation.
We conduct environmental preservation activities with recognition of the Kawasaki Plant’s location in the Keihin Industrial Zone and as a company located next to a major metropolitan area.
- We set environmental objectives and targets, and have all people who work for and work with our company engage in environmental preservation activities. We regularly conduct reviews and strive to make ongoing improvements.
- We comply with laws, ordinances, agreements, and other matters concerning environmental preservation. We set voluntary standards and strive to improve our environmental preservation.
- In addition to conventional environmental preservation activities, we strive to prevent pollution through recycling and resource and energy conservation in our production activities.
- We strive to thoroughly communicate our environmental policy through education provided to all people who work for and work with our company.
- We strive to act in cooperation and solidarity with the local community for the promotion of environmental preservation activities.
Executive General Plant Manager of Kawasaki Plant, Nippon Yakin Kogyo Co., Ltd.
Climate Change Countermeasures
The steel industry is an energy-intensive industry. At Nippon Yakin Kogyo, we believe that addressing climate change is a management issue of ours as a member of the steel industry, and are proactively working for carbon neutrality to fulfill this social responsibility.
Our CO2 emissions reduction targets
In December 2021, we set a CO2 emissions reduction target of 46% for FY2031 (Scope 1 + 2, compared to FY2014), and aim to achieve net zero emissions by FY2051. In Medium-Term Management Plan 2024, which we announced in May 2023, we established a plan to achieve our 46% reduction target in FY2026, ahead of FY2031. We are also promoting initiatives to achieve carbon neutrality throughout the entire Nippon Yakin Kogyo Group.
CO2 emissions reduction targets(Scopes 1 + 2)
Roadmap to carbon neutrality
Nippon Yakin Kogyo formulated a roadmap to achieve carbon neutrality by FY2051.
We aim to facilitate the usage of recycled materials at Oheyama Plant to establish a carbonless operation technology targeting Scope 1 emissions. We will strengthen the shift to LNG and other energy along with working on installation of a new synthetic methane/hydrogen combustion system.
As for Scope 2 emissions, the new electric arc furnace contributes to energy conservation.
We will consider introducing green power in the near future during the renewal of equipment, one of which is being equipped with an inverter controller. We will consider conducting carbon offset activities for CO2 emissions in order for us to implement all possible countermeasures for energy saving and emissions (from purchased products and services) accounting for 75% of the total.
Roadmap to carbon neutrality
Progress with measures
Nippon Yakin Kogyo has been thoroughly implementing energy saving countermeasures in all the business activities. We use the devices equipped with inverters and LED lamps at Kawasaki Plant. We also began operating an efficiently energy saving electric arc furnace (“E furnace”) in the plant in January 2022.
Moreover, we began operating a system responding to demand enabling flexible operation according to changes in the electricity supply demand balance. In addition, since FY2023, we have been operating an internal carbon pricing (ICP) system to set carbon prices and virtually convert our CO2 emissions into monetary costs for capital investment to reduce our CO2 emissions.
We announced that we would embrace the challenge of carbonless nickel smelting at Oheyama Plant producing ferronickel alloys as the major material for stainless steels. We extended the use of materials recycled from “urban mines” to decrease per unit of fuel to suppress the CO2 emissions to meet this challenge.
The total amount of CO2 emissions for FY2024 from Nippon Yakin Kogyo on a non-consolidated basis came to 310,000 tonnes including emissions from Kawasaki and Oheyama Plants. The amount of emissions from the entire Nippon Yakin Kogyo Group totaled 337,000 tonnes. It is generally recognized that the amount of CO2 emissions significantly depends on the amount of production. However, we are aiming at achieving our reduction targets by steadily decreasing per unit emissions.
CO2 emissions from the entire supply chain
In order to grasp the amount of CO2 emissions generated across the entire supply chain that supports our business activities, we are estimating our Scope 3 emissions based on the basic guidelines (Ver. 2.6) for the estimation of greenhouse gas emissions across the supply chain published by the Ministry of the Environment and the Ministry of Economy, Trade and Industry.
GX League
GX League is a forum promoted by the Ministry of Economy, Trade and Industry as a venue for government-academia collaborations by companies working on sustainable growth with the aim of achieving Japan’s goal to be carbon neutral by 2050. Nippon Yakin Kogyo announced its entry into the GX League in March 2024.
Risks and opportunities posed by climate change
For the creation of a decarbonized society, each country has announced their respective greenhouse gas emissions reduction targets. We likewise regard the risks and opportunities posed by climate change as important issues for our own sustainability. Accordingly, we have analyzed the risks and opportunities in line with the recommendations made by the Task Force on Climate Related Financial Disclosures (TCFD).
The Sustainability Strategy Promotion Committee chaired by the president leads the execution of a plan do check act (PDCA) cycle for the risks and opportunities posed by climate change, fosters relevant measures for the entire company, and reports the details as necessary to the Board of Directors.
We conducted scenario analysis for the 4℃ scenario (the projected outcome if no measures against climate change are taken) and the 1.5℃ scenario (the outcome if the average temperature increase in this century is limited to 1.5℃). We predicted the worldwide situation in 2030 based on each of the scenarios and identified the risks and opportunities, and then divided the identified risks into transition risks and physical risks.
For transition risks we referred to the IEA World Energy Outlook for future energy supply and demand and carbon pricing and for physical risks we referred to the hazard maps created by local governments. By using these materials, we quantified the impact of the risks on our business to make impact assessments. Also, each of our departments discussed countermeasures against the risks. The following table shows the results.
Against this backdrop, in September 2022, Nippon Yakin Kogyo announced the support for the TCFD’s recommendations. Going forward, we will conduct more detailed examinations for the scenario analysis and continuously enhance our climate change countermeasures while disclosing the related information to the public.

Scenario analysis results
Scenario |
Impact assessment item (Social changes) |
Impact assessment* | Risks and opportunities | Countermeasures | |
---|---|---|---|---|---|
4℃ | 1.5°C | ||||
Transition risk | Introduction of carbon pricing Policies Laws & RegulationsMarket |
Large | Increase in the manufacturing cost due to the additional cost caused by carbon pricing |
|
|
Shift to a carbon neutrality-oriented society TechnologiesMarketReputation |
Large |
|
|
||
Increase in the amount of capital investment for CO2 emissions reduction |
|
||||
Shrinkage/elimination of demand in fields with large CO2 emissions (Flue gas desulfurizers for low-efficiency coal-fired thermal power plants, boilers and EGR systems) |
|
||||
Large | New demand in the environment- and energy-related fields | ||||
Tight supply of recycled materials |
|
||||
Physical risk | Impact of abnormal weather events on business Acute |
Large | More frequent and intense natural disasters (heavy rain, strong winds and storm surges) that cause the suspension of production, fragmentation of the supply chain and the suspension of logistic services |
|
|
Degradation of the working environment due to rise in temperature Chronic |
Expanded risks of health damage caused by infectious diseases and heatstroke |
|
※ ▼:Risks、▲:Opportunities、ー:No or few impactsp>
Reduction of Environmental Impact
Preventing air pollution
We regularly monitor the air emissions discharged from our plants according to the related laws to manage and improve them. At Oheyama Plant, we combined a wet type precipitator and an electrostatic precipitator to decrease particulate matter, and are appropriately managing this equipment. At Kawasaki Plant, we have taken measures such as applying a burner with low NOx for a furnace and trying to reduce emissions of nitrogen oxides.
Release of nitrogen oxides into the air
Preventing water pollution
Water used in our production processes is released out of the plant after being treated at our wastewater treatment facilities so as to meet all the regulatory standards relevant to prevention of water pollution. Water at Kawasaki Plant is constantly monitored for contaminants (nitrogen, phosphorus, COD).
COD of water released into the environment
Management of chemical substances
We quantify the amounts of pollutants released and transferred into the environment (air and public waters) from our sites according to the pollutant release and transfer register (PRTR) system*. We annually submit a report on the released amount to the national government continuously ensuring the most appropriate control of chemical substances. We stock PCB waste in an appropriate manner coinciding with the plan to complete the management by the deadline indicated by the national government based on the Act on Special Measures concerning Promotion of Proper Treatment of PCB Waste.
Release and transfer of substances regulated under the PRTR system
Effective use of by-products
We utilize the ferronickel slag and stainless steel making slag, by-products from Oheyama Plant and Kawasaki Plant, respectively, as substitutes for concrete aggregate in roadbed materials. The effective use of slag also significantly contributes to the conservation of natural resources.
JIS certification for ferronickel alloys slag used as concrete aggregate
NASSAND is the ferronickel slag generated at Oheyama Plant and it is certified as concrete aggregate material under JIS-A-5011 (Slag aggregate for concrete – Part 2: Slag aggregate for ferronickel alloys slag).
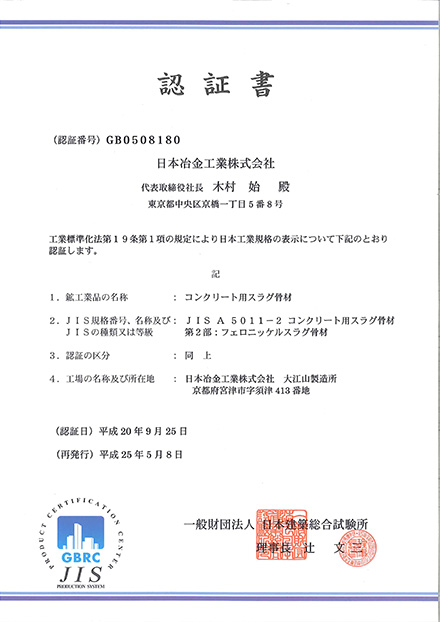
NASFINESAND
NASFINESAND is produced from the ferronickel slag generated in the unique nickel ore smelting process at Oheyama Plant. The slag is granulated into fine particles (with diameters of 75μm or smaller) which composes 90% of NASFINESAND. This material can be widely applied for embankment, backfilling, land development, foundation for drainage and the use of heavy machinery. The material produced by our unique method has already been patented and registered with the New Technology Information System (NETIS) of the Ministry of Land, Infrastructure, Transport and Tourism.
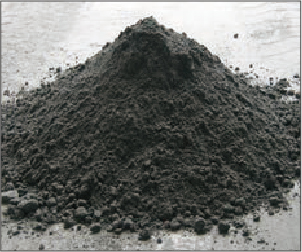
Stainless-steel slag: NASFILLER certified under the Low CO2 Kawasaki Brand and Kawasaki Mechanism Certification Systems
Stainless steel slag generated from Kawasaki Plant, called “NASFILLER,” is certified as a product made in Kawasaki, contributing to reduction of CO2 emissions throughout the life cycle under the Low CO2 Kawasaki Brand Certification System and the Kawasaki Mechanism Certification System.
(Low CO2 Kawasaki Brand : https://www.k-CO2brand.com/ )
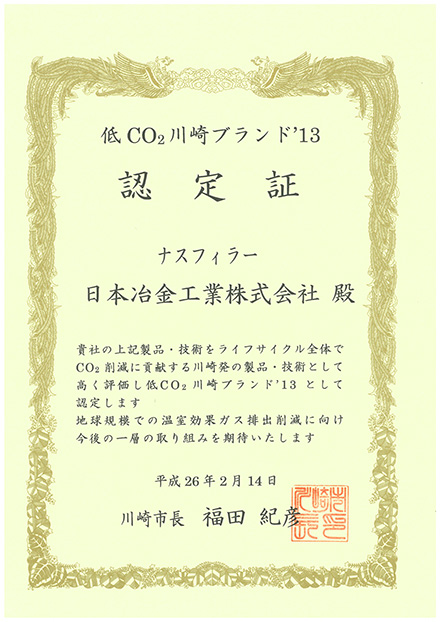
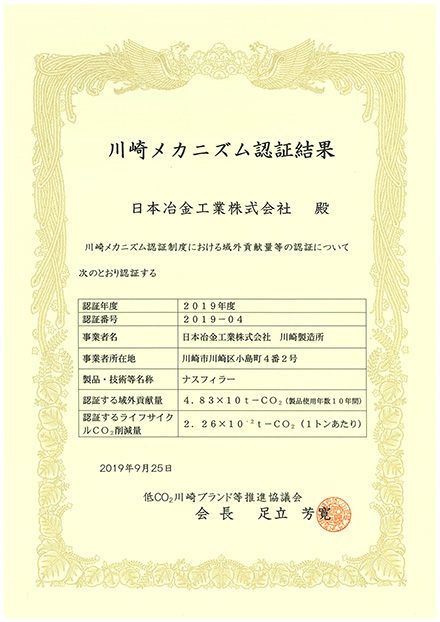
Waste generation
Nippon Yakin Kogyo has been suppressing the generation of industrial waste and promoting the recycling of such waste to reduce the final disposal amount.
Final disposal amount of industrial waste generated
Building a Recycling-Oriented Society
Stainless steel is 100% recyclable and collectible as scrap for recycling. We apply the raw materials reclaimed from “urban mines” to minimize the impact on climate change and the environment while supporting the prosperity of society.
Usage rate of recycled materials
At our Oheyama Plant, we produce ferronickel alloy as the major raw material to produce stainless steels. Nickel is a
precious mineral resource that has been designated by the Ministry of Economy, Trade and Industry as a critical mineral.
In the past, all of our raw nickel materials were nickel ore imported from outside Japan, but we are now working
to expand our use of recycled materials from urban mines.
In FY2024, our usage rate of recycled materials reached 58.7%, but we are aiming to reach 100% in future.
The usage rate of recycled materials at our Kawasaki Plant is currently around 80%. In addition to urban-mined
ferronickels produced at our Oheyama Plant, materials used to produce stainless steels at our Kawasaki Plant include
scrap stainless steel and ferrochromium. In future, our Kawasaki Plant will work together with our Oheyama Plant
to diversify its raw materials and further improve its usage rate of recycled materials.
Water recycling
As an important resource we recycle water in our production processes. The recycling rate attained is more than 70% and more than 90% at Oheyama and Kawasaki Plants, respectively.
Recycling of sludge and dust
In the stainless steel process, byproducts are generated including dust from the electric arc furnace and sludge from the pickling process of wastewater treatment. They contain valuable metals including iron, chromium, nickel, molybdenum and others. We mix these with water and knead them into briquettes, which are then melted in an electric arc furnace to extract the valuable metals by separating slag. The valuable metals are collected to help produce stainless steels.
We installed a new briquetting machine in 2012 with equipment to add binder to strengthen the briquette. This investment also contributed to the recovery rate of valuable metals. We applied the subsidy provided by the national government for companies using rare earths for the installation. This equipment allowed us to operate the submerged arc furnace at higher temperatures to increase the recovery ratio.
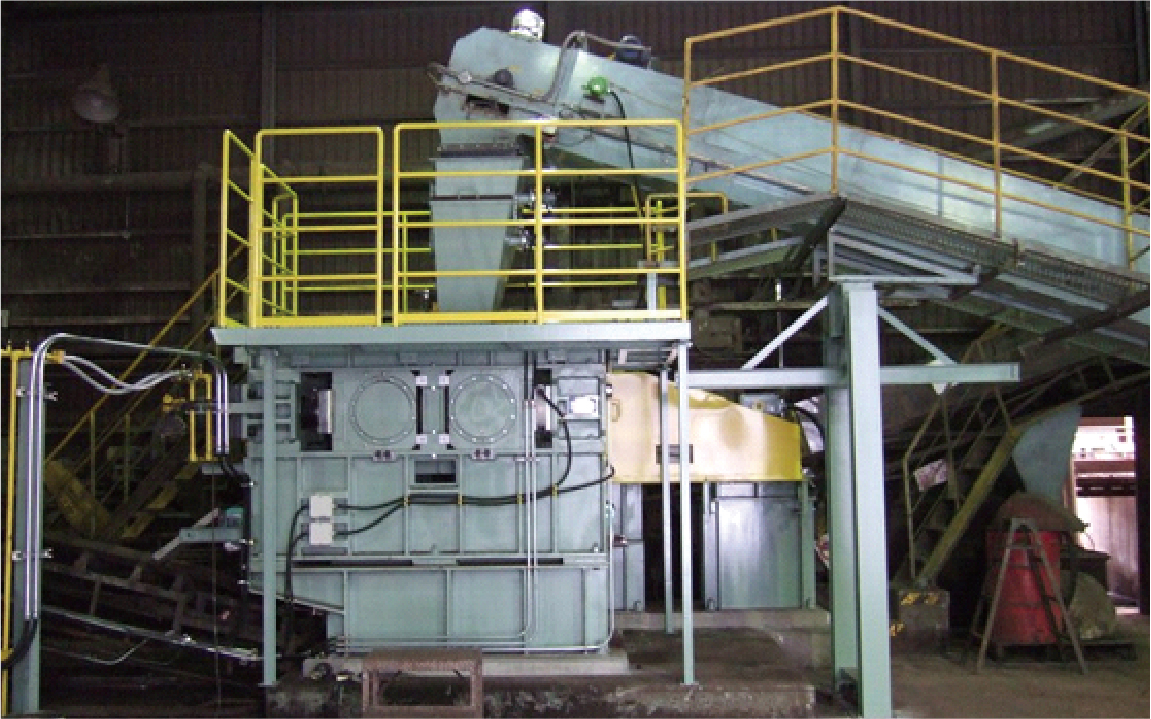
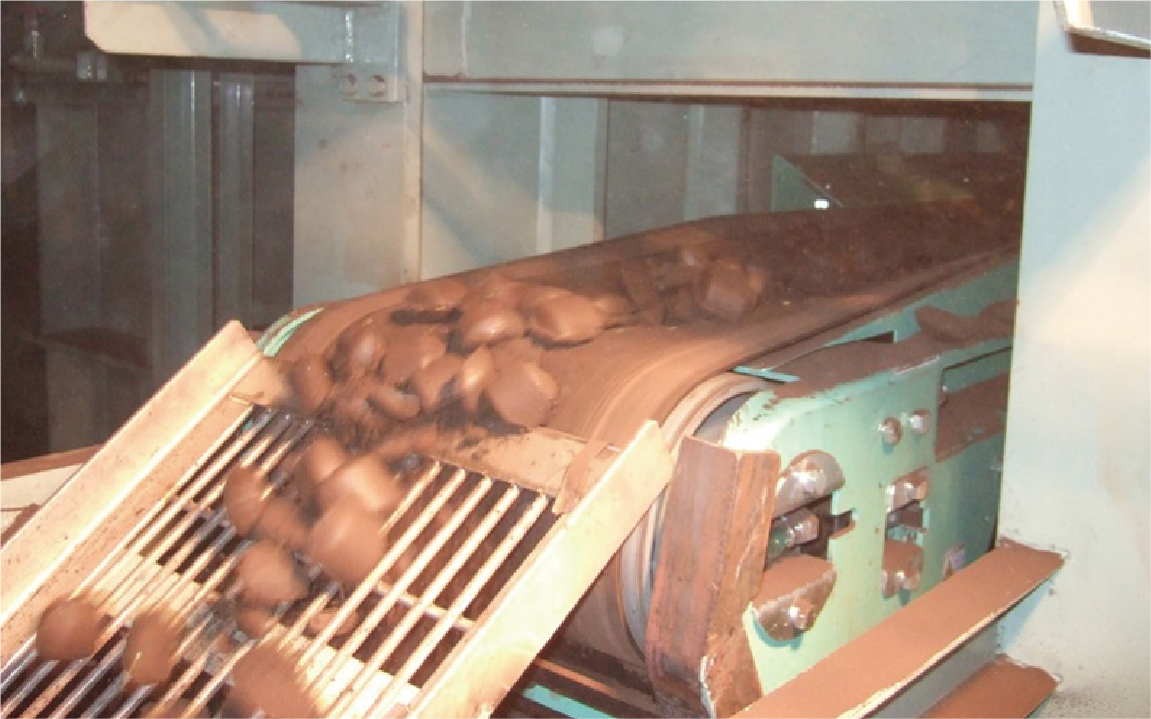
Material Flow
Results for FY2024
We mainly use the recycled materials in our processes effectively contributing to the creation of a recycling-oriented society. We are proactive in use of materials extracted from stainless steel scrap widely available in society together with materials from so-called “urban mines.” We are also making an effort to improve our technology through capital investment allowing us to offer more value to society. We have developed our own in-house recycling process efficiently using the byproducts generated in our production processes. We are also considering new applications for the byproducts. For example, we are working on the recycling of slag into a roadbed material for sale outside the company.