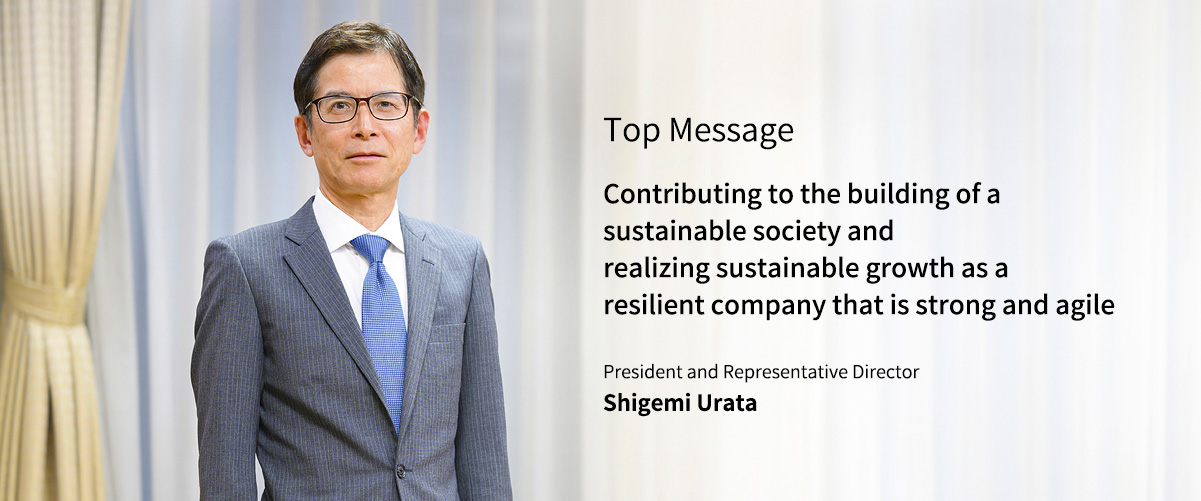
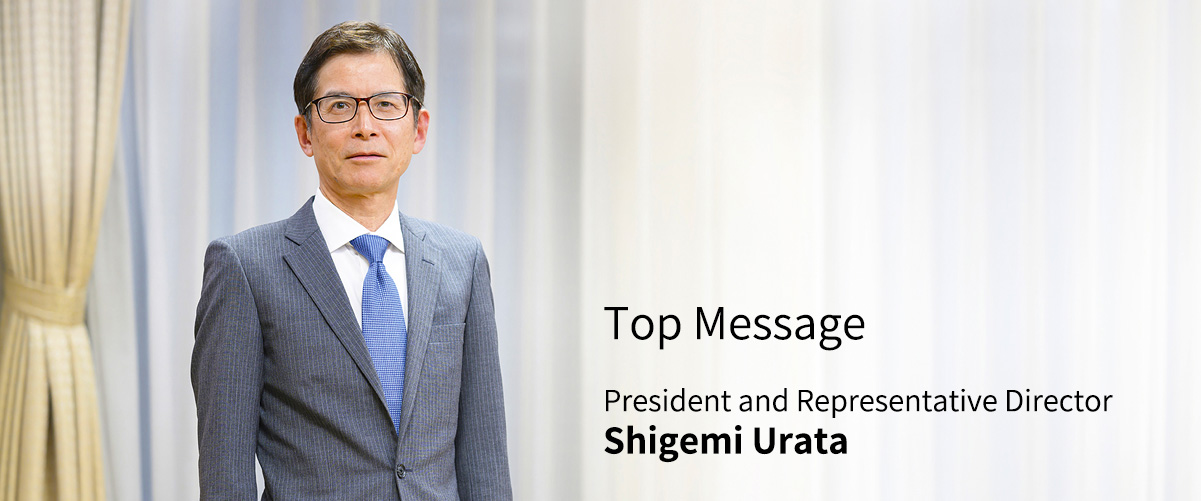
Contributing to the building of a sustainable society and
realizing sustainable growth as a resilient company that is strong and agile
At present, the fact that we have many different products in the high-performance alloys area is a strength of the Company, and has even strengthened our relationships with both domestic and overseas customers. Gaining customers’ trust is the absolute most important factor in the sustainability of a business. The products we handle are materials that provide support in people’s daily lives and can even contribute to the realization of a carbonless society.
We need to make sure our customers properly understand that value. We also need to make sure our employees have a sense of confidence and pride in the fact that we are known by society for making good products. And it is also important to reward our shareholders. To create that positive cycle of value, we will continue to fulfill our responsibility to provide the products society needs in a timely manner and continue to earn our customers’ trust.
Aiming to be a resilient company with diverse products and personnel
The conditions of this industry are changing dramatically, and there are many cases where our capabilities are not enough. But no matter how tough things are, we have shared our respective wisdom and done everything we can.
As long as we remain in this business, we will need to be indomitably agile and tenacious enough to prevail amid difficulty. This is why we resolve to be a “resilient company”. “What we aim to be in 2030” encompasses “Resilience”, based on the importance of using the diversity of our materials, our products, and our personnel to our advantage in difficult environments, and “Sustainability”, with a view to sustainable business operations.
Stainless steels and high-performance alloys have long lives due to their resistance to rust, and they are also easy to recycle. Both of these factors are advantageous when it comes to life cycle costs. At the same time, they are materials that contribute to reduction of environmental impact, so there are high hopes for these materials in the age of sustainability and the SDGs. Characteristics such as their corrosion resistance, heat resistance, and low thermal expansion are particularly needed in renewable energy and new energy fields such as hydrogen, and we can expect to see a significant expansion of the areas where our products are used. Provision of socially useful products in these ways are a priority for me, and as such, I want to increase the ratio of high-performance alloys in our net sales.
We believe that achieving carbon neutrality and expanding our production and sales of high-performance alloys are critical issues for the Company to work on.
Investment in strategies to these ends is a major angle of our current Medium-Term Management Plan, and we have designated reorganizing our product portfolio to ensure diversity in our products as another important initiative. As I mentioned earlier, quickly changing tack to a strategy centering on high-performance alloys in response to an oversupply of stainless steel products enabled us to find a new road to growth in the past.
We must also consider that our current and future employees are the ones who will actually carry out our initiatives to achieve “What we aim to be in 2030”. The diversity of our personnel is also a key theme in our human resources strategies. It is clear that diversity in our organizations and personnel is useful for coming up with ideas, creating technological innovations, and adapting flexibly to changes in our external environment.
The Company will continue to provide multifaceted support through measures such as implementing human resource development systems that respect personnel’s individuality and enable them to develop their diverse capabilities based on a corporate culture that fosters active communication between diverse personnel. I want to create an environment where every employee feels a sense of pride and fulfillment in their work, which will increase motivation and engagement and lead to ongoing improvement of our corporate value.
Anticipation of changes in our external environment and a view to our future businesses
There are various changes in our environment that pose risks to the Company, including geopolitical risks such as the situation in Ukraine as well as increases in material prices and energy costs, the weakening of the yen, and chronic labor shortages. We are aiming to build a business structure that can withstand changes, but we are paying particularly close attention to the stagnation of the Chinese economy, the influx of imported stainless steel into the Japanese market, and environmental changes being made to realize a decarbonized society.
We can assume that the stagnation of the Chinese economy will have an immense impact on the Company since half of our exports of high-performance alloys are to China. No improvement in the Chinese economy is forecast at present, but we are not despairing, as there is still potential for opportunities such as ongoing demand in solar energy and the expansion of hydrogen energy. However, from a risk diversification perspective, I believe that there is an urgent need to gradually reduce our dependency on the Chinese market and fully advance into the Indian market, where we can expect to see growth in the environmental and energy fields. At present, our Singaporean subsidiary handles sales activities for the Indian market, but we are preparing to establish a base in India in the first half of 2025 to strengthen our promotional framework. Obviously, since this is an overseas business, we will pay close attention to elements such as differences in business customs and taxation, and proceed with care.
In terms of the influx of imported stainless steel in theJapanese market, which is becoming a fixture, we need to act with increased concern, as this situation could jeopardize the Company’s survival if it worsens. To maintain sound and fair trade, it goes without saying that it is ideal for companies to maintain mutually beneficial relationships with the countries where they are exporting their products to prevent excessive harm to those countries’ local industries.
With regard to changes in industry structures and regulations with the aim of realizing a decarbonized society, the focus has been on changes caused to industry structures by the transition from gasoline-driven vehicles to EVs, but since the ratio of our stainless steel that is used for automobiles is by no means high, the impact of this transition will be limited. Meanwhile, our high-performance alloys are increasingly being adopted in solar power generation, geothermal power generation, and water electrolysis facilities for hydrogen energy. This is a major, growing business opportunity. We aim to develop new materials, build an efficient production framework, and capture demand in the Indian market. The need for green steel materials with limited CO2 emissions is also growing globally, and like at many companies, discussions are underway to adopt these and expand our business for them.
With regard to our Basic Strategy 2 to improve our capabilities for sustainable procurement and strengthen our cost-competitiveness, we have increased our use of recycled materials from “urban mines” (discarded batteries and catalytic materials) as part of our measures to diversify our raw materials and avoid procurement risks associated with the nickel ore used as a raw material. In FY2024, recycled materials reached a ratio of 58.7% of our materials.
Recycled materials contain more nickel than nickel ore, reducing fuel usage per unit during smelting. This has enabled us to reduce energy costs and CO2 emissions, which has also helped to strengthen our cost competitiveness. Additionally, we are contributing to a circular society, as materials that would otherwise have been disposed of are being recycled and used effectively.
An issue we are facing is that these materials are extremely difficult to handle: there are over 200 kinds of recycled items and they cannot be used as they are; they need to be treated before they can be used in our production processes. To address this issue, we are improving handling processes after receiving the items, such as analysis, as well as adjusting the composition to ensure consistent quality for the finished products, refining elements such as our technology for reclaiming nickel, and conducting ongoing prototype testing to increase our ratio of recycled materials.
With regard to our Basic Strategy 3 to utilize DX to improve operational efficiency and improve our organizational capabilities, we are steadily improving the efficiency of our operations, beginning with digitalization of analog data in our departments involved in site work. We are also working to rebuild operation management systems, including Group-wide systems. In future, we aim to standardize management platforms throughout the Group to further centralize our management functions. In future, we plan to increase our personnel to facilitate a faster transition to DX. We are currently formulating strategies and roadmaps with specialized external consultants evaluating our current situation and providing advice.
In FY2024, we fully migrated our operation management system to an open platform. This will make it easy to utilize advanced IT systems such as AI in future, and we also expect to see a dramatic decrease in the operating costs of our operation management system and costs involved in securing engineers to maintain it.
Message to our stakeholders
As the stainless steel industry is easily impacted by conditions in material markets, our results fluctuate significantly, and we have experienced countless difficult situations in the past.
Words cannot express the depth of my respect and gratitude to my predecessors who have worked so hard to pass the baton and keep the Company in business to this day, and the many people who have lent us a hand.
I am conscious that a critical business issue we must tackle is building a resilient and sustainable business structure that will not be severely impacted by the economic situation surrounding it. In light of this, our 100-year anniversary in 2025 is not a finish line; it is merely a milestone. I believe that we need to think further ahead and grow over the 100, 200 years that follow.
When Hisashi Kubota, our previous President, was appointed, he said that he wanted to pass the baton adeptly to the next generation. I feel the same way now. I will dedicate myself to the development of the Company so that we can continue producing products based on the needs of our customers and markets and be a company where our employees will be proud to work. I humbly ask for the ongoing understanding and support of all of our stakeholders.